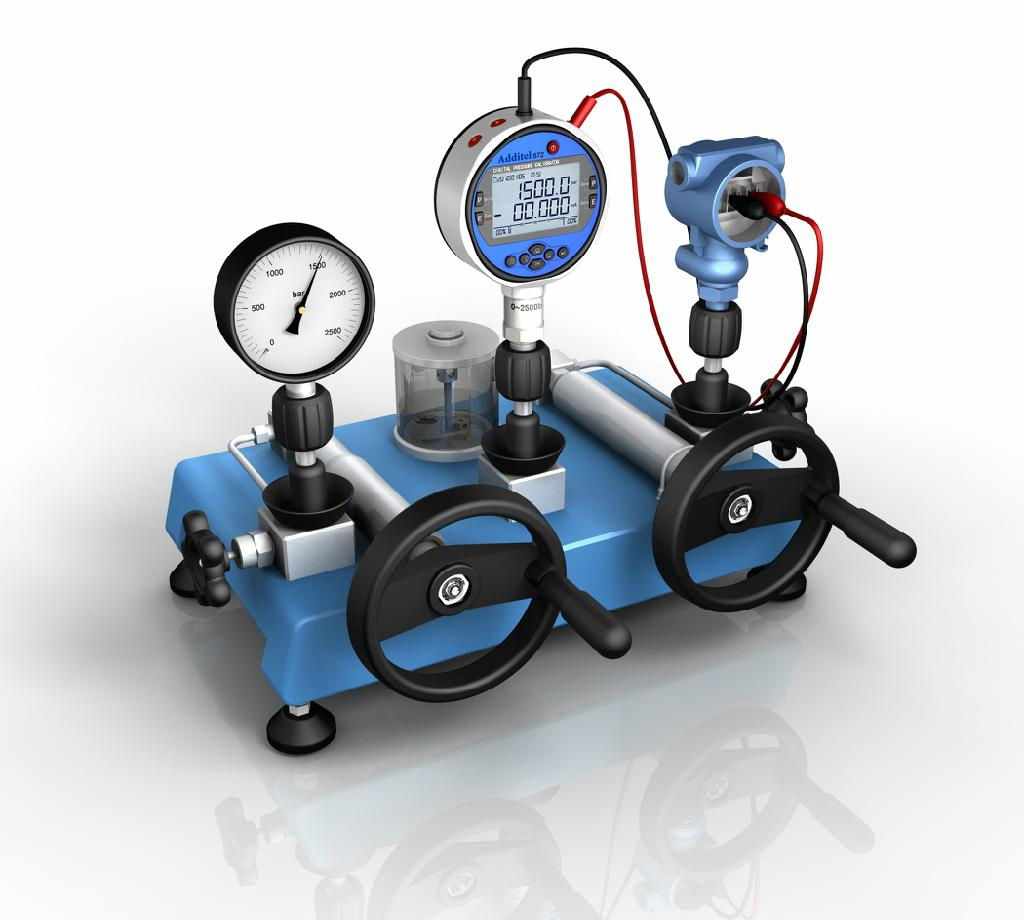
Precision is key in the world of manufacturing. Every product, from automotive parts to electronic components, relies on exact measurements to ensure its quality and performance. One crucial aspect of maintaining this precision is pressure calibration. But how does this seemingly technical process influence the final product? Let's explore the world of Pressure calibration services and its impact on product quality.
What is Pressure Calibration?
Pressure calibration is adjusting and verifying pressure measurement instruments to ensure they provide accurate readings. This involves comparing the instrument’s measurements to a known standard and making adjustments as necessary. Calibration helps maintain the reliability of pressure gauges, sensors, and other instruments used in manufacturing processes.
The Role of Pressure Calibration in Manufacturing
Ensuring Accuracy
Even the smallest deviations in pressure can lead to significant issues in manufacturing. For instance, accurate pressure readings are vital in the production of precision-engineered components. Pressure calibration ensures that instruments used to measure and control pressure are accurate, which helps produce parts that meet stringent specifications. Without proper calibration, there’s a risk of producing defective products, which can lead to costly rework or recalls.
Improving Product Consistency
Consistency is essential in manufacturing. Pressure calibration is key in ensuring products are consistently produced to the same standard. By regularly calibrating pressure measurement instruments, manufacturers can minimise variations in product quality. This is especially important in industries like pharmaceuticals, where consistency in pressure is critical to ensuring that products meet safety and efficacy standards.
Reducing Waste and Costs
Accurate pressure calibration can reduce waste and operational costs. Properly calibrated pressure instruments minimise the chances of producing defective products that must be scrapped or reworked. This not only reduces material waste but also saves time and money. For manufacturers, this means more efficient operations and better profitability.
The Calibration Process
Initial Calibration
Before an instrument is used, it undergoes an initial calibration. This ensures that it provides accurate measurements from the start. Initial calibration involves comparing the instrument’s readings to a known pressure standard and adjusting as needed.
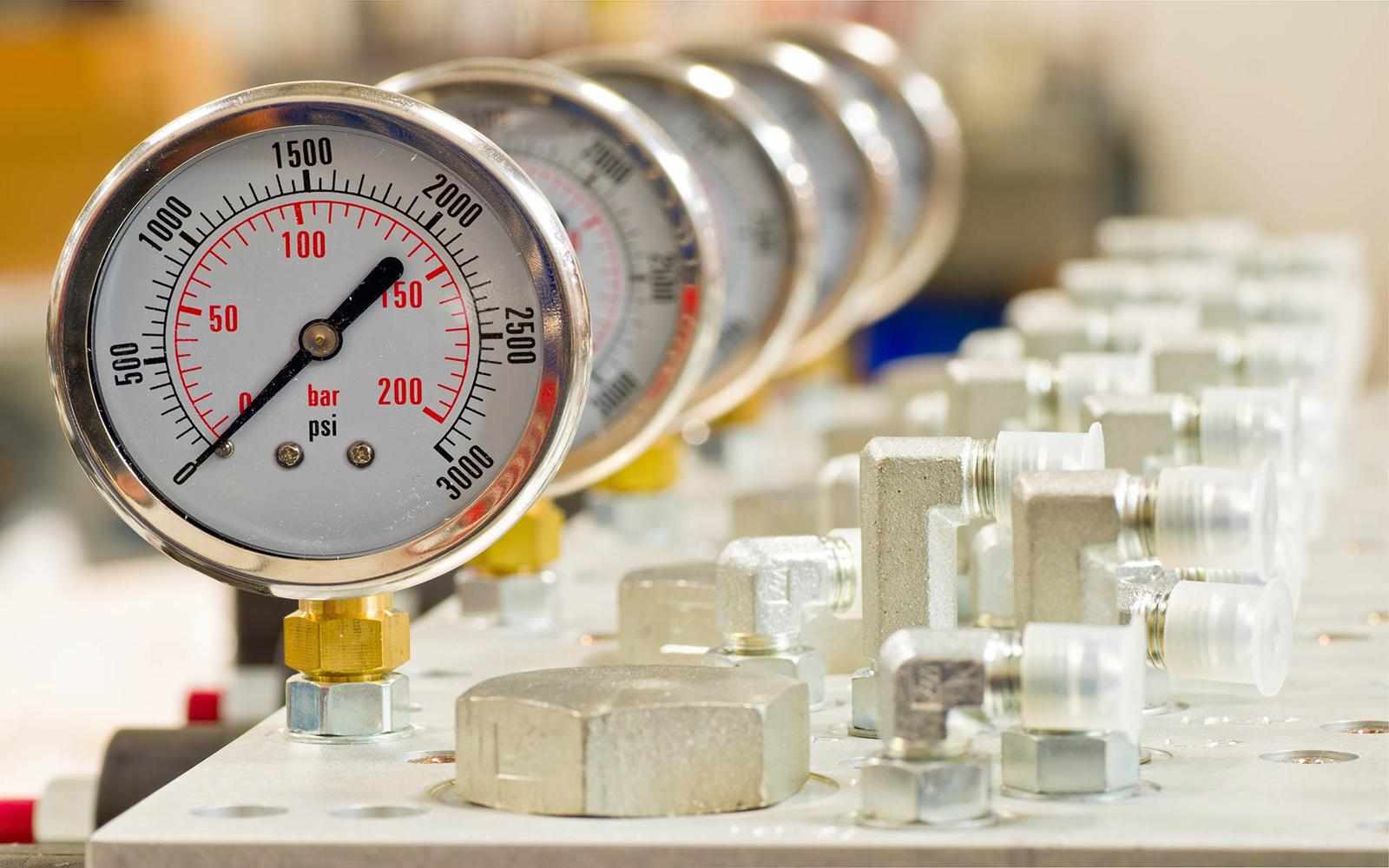
Routine Calibration
Once an instrument is used, routine calibration is required to maintain accuracy. The frequency of routine calibration depends on factors such as the instrument’s usage, the environment in which it operates, and the manufacturer’s specifications. Regular checks and adjustments help ensure that the instrument performs accurately over time.
Verification and Documentation
Verification is an essential part of pressure calibration. It involves confirming that the instrument meets the required accuracy standards after calibration. Documentation of calibration results provides a record of the instrument’s performance and any adjustments made. This documentation is crucial for quality control and compliance purposes.
The Benefits of Regular Pressure Calibration
Enhanced Quality Control
Regular pressure calibration supports effective quality control by ensuring that pressure measurements are accurate and reliable. This leads to higher-quality products and helps maintain the manufacturer's reputation for producing reliable and consistent products.
Compliance with Standards
Many industries have strict regulations and standards that require regular calibration of measurement instruments. Adhering to these standards helps manufacturers avoid penalties and ensures that their products meet industry requirements.
Increased Longevity of Equipment
Proper calibration can extend the lifespan of pressure measurement instruments. Manufacturers can prevent premature wear and tear by ensuring they are operating correctly and making necessary adjustments, reducing the need for frequent replacements.
Conclusion
Pressure calibration may seem small in the vast manufacturing world, but its impact is far-reaching. From ensuring accuracy and consistency to reducing waste and costs, the role of pressure calibration in maintaining product quality cannot be overstated.
Manufacturers can enhance their quality control processes by investing in regular calibration practices, complying with industry standards, and delivering superior products. So, the next time you encounter a perfectly crafted product, remember that behind its quality is the crucial pressure calibration process, working tirelessly to ensure every detail is right.
Write a comment ...